
Freeze drying, also known as lyophilisation, is a common method of preservation used in many products, from the fresh herbs and vegetables that top store-bought pizzas to the instant coffee in our morning brew. Another industry that relies on this concept is pharmaceuticals, particularly in the production of delicate, high-value injectable products. Many pharmaceutical products are sensitive to heat, therefore the ability to dry contents at low temperatures is a clear advantage.
Vacuum technology is essential in the lyophilisation process. After the goods have first been frozen, a vacuum reduces the pressure until sublimation takes place. Most of the moisture is removed during the primary drying stage. Secondary drying removes adsorbed residual moisture until the target value is achieved, at which point the material is secured in a moisture-free package.
The development of a robust drying system for lyophilisation requires four key components: vacuum pumps, pressure gauges, mass spectrometers, and leak detectors. Pfeiffer Vacuum’s comprehensive portfolio of technologies includes high-quality options for all of the above, simplifying procurement with a wide range of solutions from a single source.
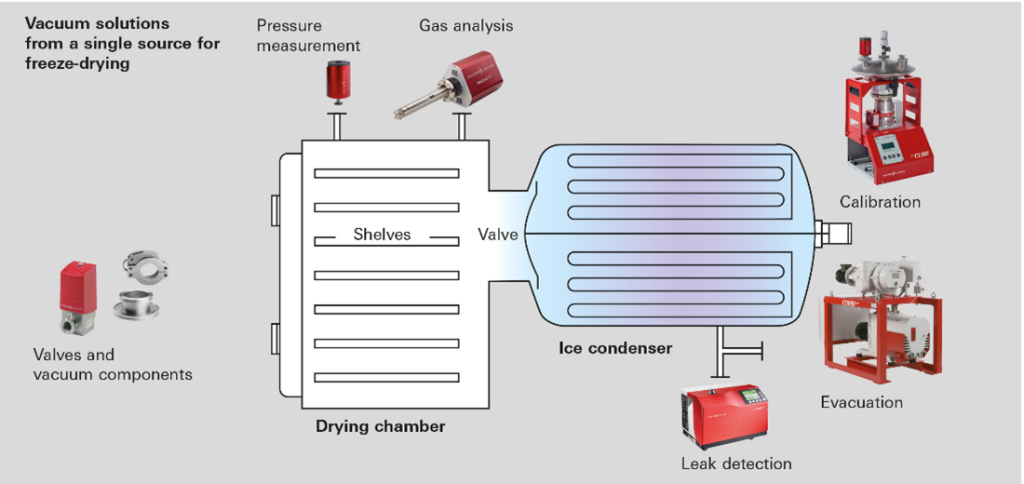
Vacuum generation
Freeze drying requires powerful vacuum pumps. The majority of the drying takes place at pressures between 0.5 hPa and 10-2 hPa, although much lower pressures may be required for the final stage. High pumping speeds are important for achieving the necessary pump-down time. Meanwhile, due to the lengthy duration of the sublimation, a reliable, low-maintenance vacuum pump is essential.
Rotary vane pumps have been the standard for many decades due to their low investment costs, robust construction, and good final pressure. Examples include the DuoLine or HenaLine pumps from Pfeiffer Vacuum. The compact DuoLine system even comes with the option for wear-free magnetic coupling, which eliminates the risk of oil leaks.
While oil-lubricated rotary vane pumps remain a popular choice, there is an increasing trend towards dry compressing options, which can even be combined. The coffee drying process, for example, often uses a combination of screw and root pumps. In these pump designs, no lubricant can mix with the pumped gases, enabling long operating hours with less oil changes. This translates to a lower cost of ownership for customers, as well as improved cleanliness.
Dry compressing pumps from Pfeiffer Vacuum include the OktaLine roots pump and HeptaDry screw pump, which stands out for its high pumping speed and optimised temperature profile. The company also offers HiLobe roots pumps – a consequent advancement of the OktaLine roots pump, using a frequency inverter and modern drive concept for powerful pump-down performance and low operating costs.
Pressure monitoring
Pressure and temperature must be tightly controlled in the drying chamber to secure consistent product quality. Highly accurate pressure gauges are required for this. When managing the freeze-drying process, Pirani and capacitance gauge technology come into consideration as they cover the pressure range relevant for the freeze drying process.
Pirani gauges represent the more cost-effective option and can achieve a practicable accuracy in the range of 10 to 10-3 hPa. These gauges are dependent on the type of gas used. The Pirani gauges in Pfeiffer Vacuum’s portfolio harness a unique Pulse technology which improves their accuracy. Generally, however, capacitive vacuum gauges with a maximum measuring range of 1 hPa or 10 hPa offer better performance and take measurements independent of gas type.
Both Pirani and capacitive gauges are included in Pfeiffer Vacuum’s portfolio. These products are sometimes combined in a process known as comparative pressure measurement – an effective method for determining the vapour content in the drying chamber. A Pirani gauge calibrated for nitrogen, for example, will show a much higher pressure for vapour. By simultaneously taking a measurement with a capacitive gauge, operators can compare the measured values to accurately calculate the water vapour content.
Regular calibration is an essential way to ensure the accuracy and repeatability of any pressure gauge. Pfeiffer Vacuum offers external calibration services to customers in accordance with stringent industry standards. Alternatively, the company can provide calibration pumping stations for on-site adjustment. This can be more cost-effective for customers calibrating a large number of gauges.
Process gas monitoring
Mass spectrometers enable complete documentation of the freeze drying process. They also play an integral role in quality assurance through the detection of silicone oil leaks. In addition, mass spectrometers like Pfeiffer Vacuum’s PrismaPro are used to monitor vapour content in the drying chamber, enabling manufacturers to determine a highly accurate endpoint for the main and subsequent drying phases.
Mass spectrometry is an important, flexible technology in lyophilisation. Whether you require a standalone manual device or a completely automated system for batch monitoring, Pfeiffer Vacuum has the tools and expertise to integrate this important technology into your process.
Detection of leaks
The importance of leak detection in the development of a robust drying system cannot be underestimated. Firstly, the ‘tightness’ of the overall system will affect its ability to achieve the necessary pressure levels. Protecting products from microbial contamination is also critical, especially when it comes to aseptic freeze drying of pharmaceuticals.
Leak detection is another area in which Pfeiffer Vacuum has great expertise. The company recommends a pressure rise method as an appropriate choice for this application. Using the universally applicable ASM 340, manufacturers can identify and localise leaks quickly and easily. The technology is available in a compact version, the ASM 310, for mobile use.
Lyophilisation solutions from a single source
From pumps, gauges, and calibration devices to mass spectrometers and leak detectors, numerous technologies are required in the development of a drying system for preserving foods, drinks, and pharmaceuticals. Pfeiffer Vacuum offers all of the above in combination with trusted advice, reliable service and technical training.
Learn more about the importance of accurate pressure monitoring in lyophilisation by watching the webinar below.