
Being situated in New Zealand is challenging enough for those in charge of wine logistics. Add global shipping-route disruptions like attacks on the Red Sea and drought in Panama and conditions can become decidedly choppy.
For Auckland-headquartered wine group Indevin, there have also been major internal changes in recent years, notably the company’s creation of its branded bottled wine (or ‘finished goods’) arm following its acquisition of Villa Maria Estate. The deal saw Indevin buy Villa Maria’s namesake brand, as well as Esk Valley, Vidal, Leftfield and Australian import business House Of Fine Wine.
This month, Indevin began bottling finished goods in-market for the first time, trialing the move with Encirc in the UK.
Just Drinks caught up with logistics and customer operations manager Tracy Malone as she returned from a trip to Blenheim, where the Marlborough Villa Maria winery has been preparing to start shipping in bulk.
Just Drinks: How has recent disruption in the Red Sea and Panama impacted Indevin’s supply chain?
Tracy Malone: Traditionally, our bulk wine was Ex Works so we didn’t look after the freight. Same with our finished goods – our delivery of branded stuff was FOB.
We recently made a change in that we are sending finished goods in bulk to the UK. So, we’ve taken charge of it and it’s like: “Oh, my goodness!”
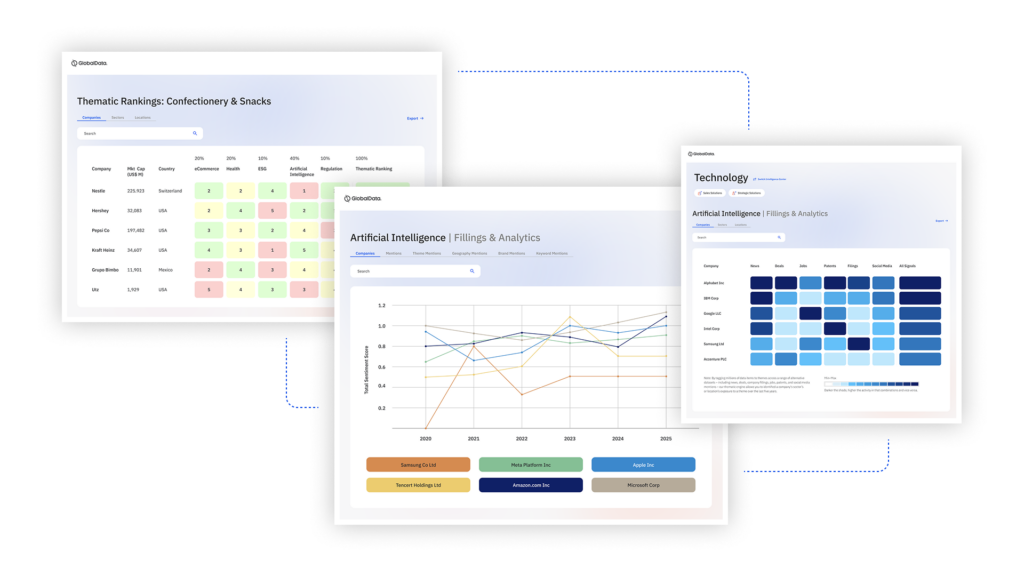
US Tariffs are shifting - will you react or anticipate?
Don’t let policy changes catch you off guard. Stay proactive with real-time data and expert analysis.
By GlobalDataHowever, we got lucky. There’s a huge cost to freight [so] we’re constantly looking at options. And one of the options that came up just a few months ago was to change shipping lines. We made the decision to go with a different shipping line via Panama and our last boats going by the Red Sea had just gone through when all of this escalated.
We were really, really lucky. But, at the same time, we were already asking those questions so it feels like an educated choice.
In Panama, they’ve got [another] problem but the ships that we’re on from New Zealand can go through the old Panama Canal, so we’re actually not impacted hugely at all.
I don’t think many people realise there’s an old Panama Canal and a new one. The new one is impacted by the drought but the old one’s actually working how it always has.
Just Drinks: What was it about your ships that meant you could use the old canal system? How do the two differ?
Malone: They are close to each other but the big one is deeper and it takes all the massive ships and cruise ships and there’s a huge displacement of water as they go through.
The ships we are on are quite long but not as deep, so they can go through that old canal quite nicely. At this stage, we’ve been unbelievably lucky.
Just Drinks: Was the decision to change routes informed by the conflict in Israel?
Malone: It was and it wasn’t. One of the key parts of my role is actually to bring options to [the table]. If we had been going solely by the Red Sea, all of a sudden we would be in quite a different position.
At that point, just before the trouble started in Israel, we were thinking about the Panama Canal and, even though the old canal isn’t affected [by the drought], it’s like, well, how long until it is? Is it quicker, is there less risk?
We were looking at all of these different things and made the decision to try the Panama route and then the trouble happened in the Red Sea.
I think quite a few of our customers who look after their own freight are now looking at that route and I’m not sure how much capacity there is now because I assume everyone’s avoiding the Red Sea as much as possible.
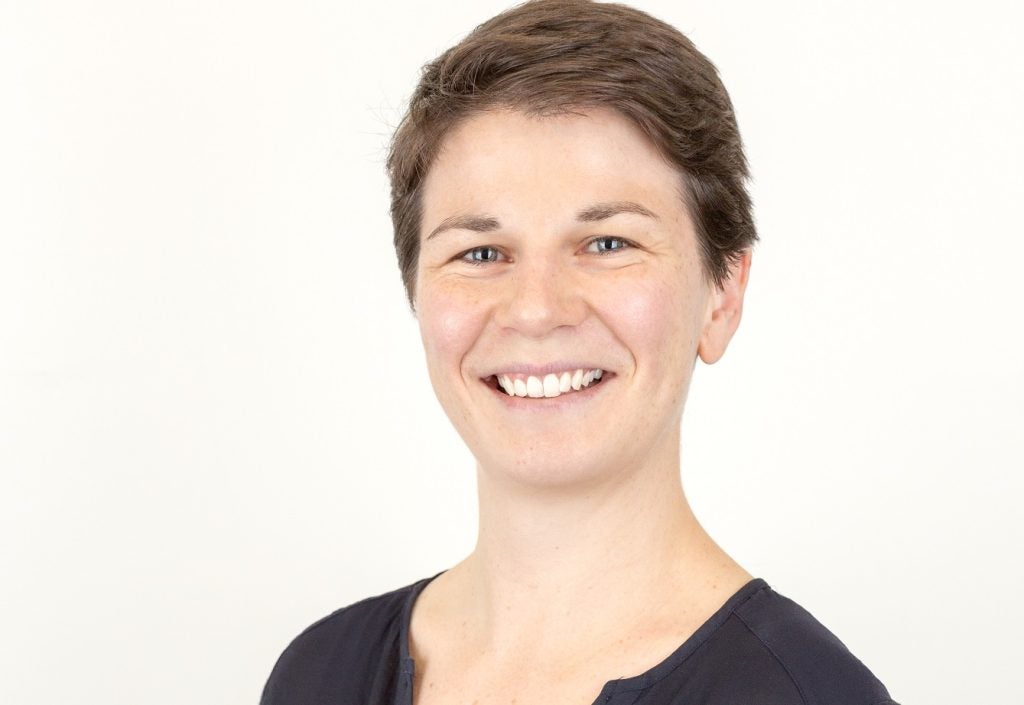
Just Drinks: Is there much of a time or cost difference for Indevin travelling via Panama?
Malone: It’s almost cost-neutral – not now but when we made the decision, it was quite cost-neutral. It’s quicker to get to the UK by Panama. Not a huge amount, I think it was five or six days but obviously it makes a difference. We’ve got a team member in the UK who’s planning things and five or six days can make a big difference to her.
With the Red Sea, that extra ten or whatever days it is to go around the Cape [some ships are re-routing around the southern tip of Africa] would have been a problem.
Just Drinks: Indevin has just started shipping those ‘finished goods’ in bulk to the UK and the first bottlings were due to be any time now. How has that project gone?
Malone: It’s going really well. We bottled for the first time this month. Everything looks amazing. My office at Villa Maria was above the bottling line, so it was always quite interesting to watch the bottling line and to see it shipped around the world but now it’s actually sent in bulk and to see it happen in-market is incredible. It’s gone to plan.
Because of Covid, our focus on logistics has changed. We’re a lot more resilient.
Just Drinks: Were there any challenges or unforeseen issues with the move?
Malone: To be honest, not really. We’ve got some really good partnerships with our suppliers and people who help us with freight, who are the experts in that field, and they’ve been fantastic at helping us get things going. Obviously, because of Covid and everything our focus on logistics has changed. We’re definitely a lot more resilient than we were because we have to be.
Just Drinks: How has the logistics industry changed since Covid?
Malone: Global logistics changed massively and reliability changed hugely. During the pandemic, our team had to plan almost day-to-day. It made us hugely resilient by building extra warehouse space and by constantly looking at options.
Reliability went out the door and now it’s coming back. We can actually plan for a week! That being said, now we’ve got the Red Sea issue but, because we have that resilience built into us from Covid, I think we’re better adapted to make those changes.
Just Drinks: To what extent was Indevin’s expertise in bulk helpful for the Villa Maria change to bulk shipping?
Malone: Hugely, of course. Indevin have sent bulk around the world for a very long time. But I guess to be honest, because we’ve partnered with people who know what they’re doing with moving freight and moving bulk wine, it’s been fantastic. It was interesting for me to watch a flexi tank get loaded with bulk wine, I’m so used to my teams filling them with glass bottles.
A flexi tank is basically a big bag of wine. A 20-foot container could take 24,000 litres of wine. They’re very sophisticated. It’s incredible, the kind of the detail that goes into filling those bags. And the quality is amazing.
Just Drinks: Do you ship your branded wines in bulk anywhere else or was the UK the first market?
Malone: No, the UK is the first. It’s only our big SKUs that we’re sending, the huge quantities.
It’ll be something that we look to do across the portfolio. It makes sense, especially for carbon emissions – sustainability is a huge focus for Indevin. Being this far away from everything, we have to have a sustainable supply chain. I think our carbon emissions to the UK have been reduced by 27% just by making this change.
We’re still going the same route. We’re still shipping the same quantity of juice. But just by doing it in a slightly different way our carbon emissions have fallen – that’s a huge drop, 27%.
Just Drinks: Will the UK bottling site supply Ireland or elsewhere in Europe in the future?
Malone: We’re open to all options. It’s so new, we’ve just started bottling but we’ll always look to see how we can do things better. If that’s a viable option, we will look at it as I’m sure we will for every market.
Just Drinks: What other sustainability initiatives is Indevin working on in its supply chain?
Malone: We only use local suppliers for bottling and packaging, so we haven’t been impacted by any of the shipping issues [in terms of raw material availability]. Using local suppliers was useful during Covid as well.
We are doing trials with lighter glass, though it’s not something I control. We already use 67% recycled glass in our products across all our branded wines. They are all bottled at the same place at the moment, in Auckland – except for the Encirc stock in the UK.
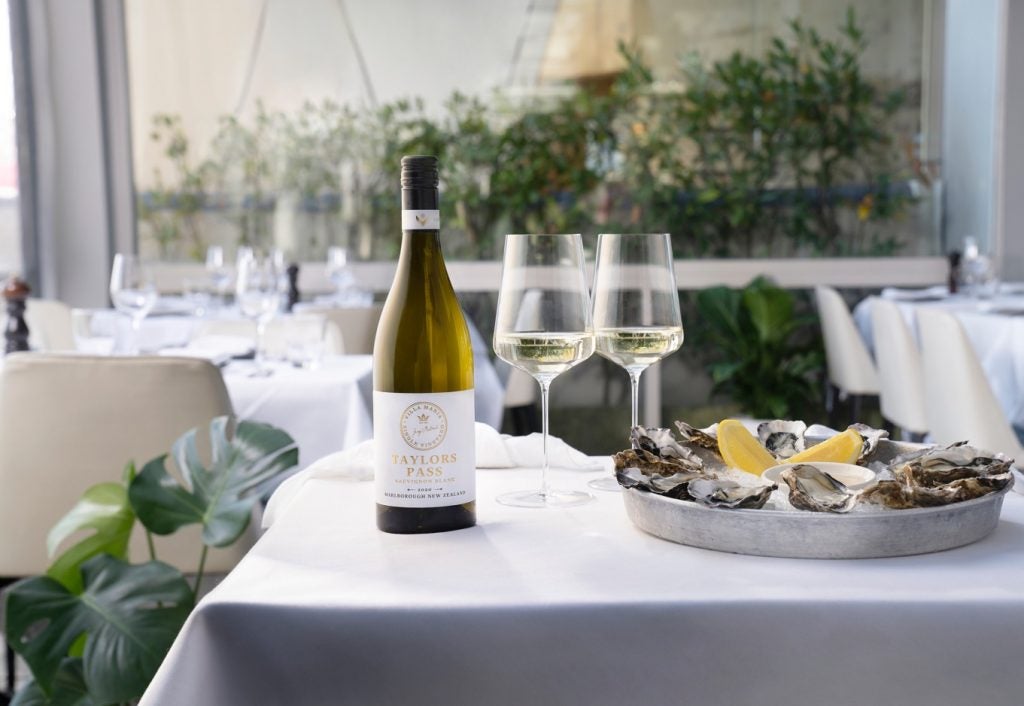
Just Drinks: How do you work with House Of Fine Wine, the distribution company in Australia, in terms of logistics?
Malone: We bottle everything in Auckland and ship it to House of Fine Wine and their various sites around Australia. My customer services team used to look after the House of Fine Wine market but they got to the point where they needed someone there [in Australia] and now do it themselves.
Just Drinks: Do you have anything to do with the end customer?
Malone: House of Fine Wine have a contract with a company called Mainfreight but it’s a group contract. We use the same company here in New Zealand.
Just Drinks: How does distribution work domestically? I remember New Zealand’s roads could be pretty hair-raising!
Malone: We’ve just moved to using Mainfreight. We used to have our own warehouse on the Auckland site for Villa Maria, for the finished goods but we’ve recently moved to using Mainfreight, which is what the House of Fine Wine team already does. One of the reasons for that is about, again, partnering with experts and the technology that they can bring.
We have a warehouse on the South Island and North Island. We use coastal shipping to send stock to the South Island. It’s actually on the international ships.
Just Drinks: What storage capacity do you have in New Zealand?
Malone: Our total bulk and finished goods capacity is approximately 100m litres (11.1m nine-litre cases).
At the moment, we’ve got around 6,000 pallets (336,000 nine-litre cases) of finished goods but that fluctuates hugely depending on the season.
A huge amount of our volume was actually bottled wine for the UK but now that we’ve moved to Encirc we are adjusting to a new finished-goods average stockholding.
Just Drinks: Do you think you might have to downsize your warehouse space?
Malone: Well, actually, stopping bottling UK wine coincided with when we went into the [Mainfreight] warehouse. We had our own warehouse on the Villa Maria Auckland site and that’s where we did our final few finished-goods boxes to the UK. There’s still dribs and drabs and we will send about five boxes a month to the UK of smaller SKUs, so that’ll continue for now.
Just Drinks: Outside Australia, do you work with different distributors in each export market?
Malone: We have a distributor in every major region: one in Ireland, one in the UK, a major one in the Netherlands. At the moment, the model for branded goods is that we send them finished wine. Indevin sends its bulk wine to similar customers.
Just Drinks: Do you sell much in Asia, and where?
Malone: We send to China, Malaysia, Japan, Singapore, Taiwan, Vietnam, Hong Kong, Korea. They’re quite small orders but those are the main ones.
Just Drinks: The last few years have been chaotic from a logistics perspective. What’s your outlook for the future?
Malone: We’ve built so much resilience into our supply chain and we’re continually looking for resilience. We’ve gone through a pandemic, now we’ve got a war and we’ve got drought and these things are just going to keep coming. We’re working to build firstly a sustainable supply chain but also one that’s incredibly resilient.
The Indevin team are just fantastic. There’s a culture of innovation, always looking for better ways of doing things.
In our space, bulk shipping is huge, just from a carbon-emissions perspective. It’s exciting times. The world’s our oyster, we just need to make sure we can get to it.